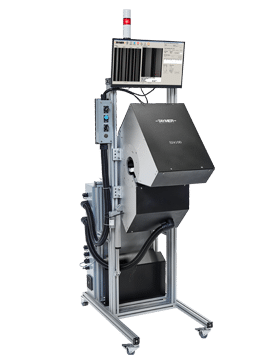
SI4100
Surface Defect Inspector for Power Cables and Large ODs
The Surface Inspector is the most thorough method of detecting surface flaws on today’s market. This system also provides dimensional measurements simplifying the QA process and allowing the operator to see the bulge or neck-down simultaneously. The camera based solution provides vision empowerment rather than older technologies like spark tester which requires defects to be exposed to the core. With the Surface Inspector you can be sure the product you are sending to your customer is free from any surface defects or imperfection.
Image Feedback and QA Improvements
The Surface Inspector provides the operator with real-time digital image feedback of the current jacket on any production line. This continuous stream of real time information – especially the failure images – allows the operator to isolate causes of jacket imperfections and where the defect is along the cable. This will result in reducing jacket defects before they result in scrapping of product or worse, customer complaints or recalls. Defect images are also saved, so they can be included in quality reports for internal or external use.
Quality Assurance
The Surface Inspector is specifically designed for a 24/7, dirty, industrial environment. The height adjustable aluminum extrusion frame allows for quick and accurate line height adjustments. A sliding rail at the base allows for lateral adjustments as well as for operators to slide the system out of the way so bulky cable joints can pass through. Covers and shields that are easy to clean prevent dust particles from entering the system. Fans, lens filter, and optional air wipes are also used to keep the whole system clean and dust free.
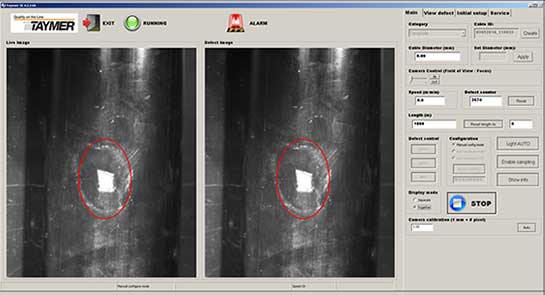
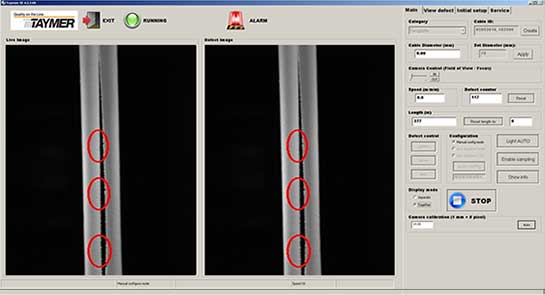
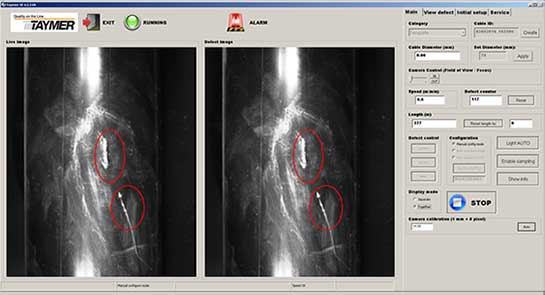
Features
- Detects pinholes, bulges, neckdowns, surface blemishes, die cuts and more on cable jacket
- 4-camera configuration housed within a singular box design
- Provides dimensional readout of measured outer diameters
- Supports line speeds up to 400 meters per minute
- Detects defects before they reach your customer or fail in the field
- Large camera-box opening for product to easily pass through
- Height adjustable aluminum extrusion frame mounted on rails to easily slide system out of the way
- Simple and low maintenance design allows the system to run 24/7
- Optional air wipes to clear cable from debris before entering the system
- Alerts and records any defects into database for QA records and operator verification
- Software analyzes full circumference and 100% of product length
Specifications
- Maximum Line speed:
400 m/min | 1,300 ft/min – Higher speed may be available depending on application - Minimum detectable defect size:
1 mm and up | 0.040” and up – Depends on line speed and product diameter - Cable Diameter Range:
30 mm – 200 mm | 1.2” – 8” – Other diameters available upon requests - Camera Configuration
4 camera – 100% coverage of very small defects - Types of Defects Detected
- Jacket defects
- Pin holes
- Neck downs
- Bulges
- Die cuts
- Pixels/mm²::
~100 for large diameter cable jacket
- Dimensions:
- 457 mm x 635 mm x 1580 mm – L x W x H
- 18” x 25” x 62” – L x W x H
- Lighting:
LED - Industrial Stand:
- Height adjustable
- Aluminum extrusion construction
- Sliding base rail
- Weight:
Aluminum extrusion construction - Options:
- Air wipes
- Encoder measuring wheel with pivot arm