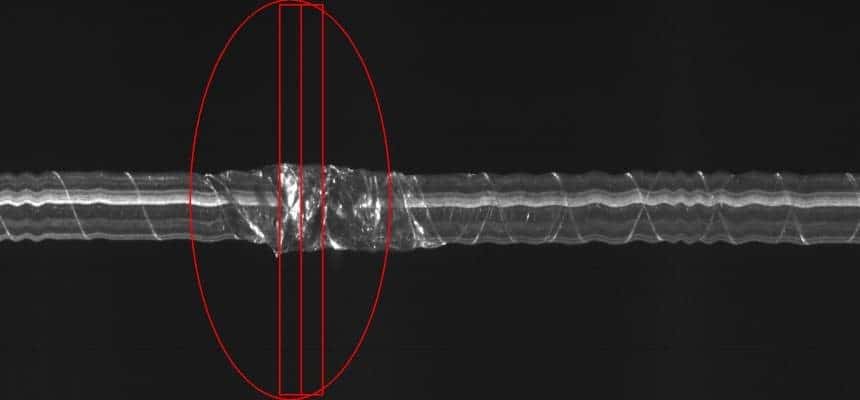
IWCS 2015 – Optical Wrap Defect Inspection for Cable
October 23, 2015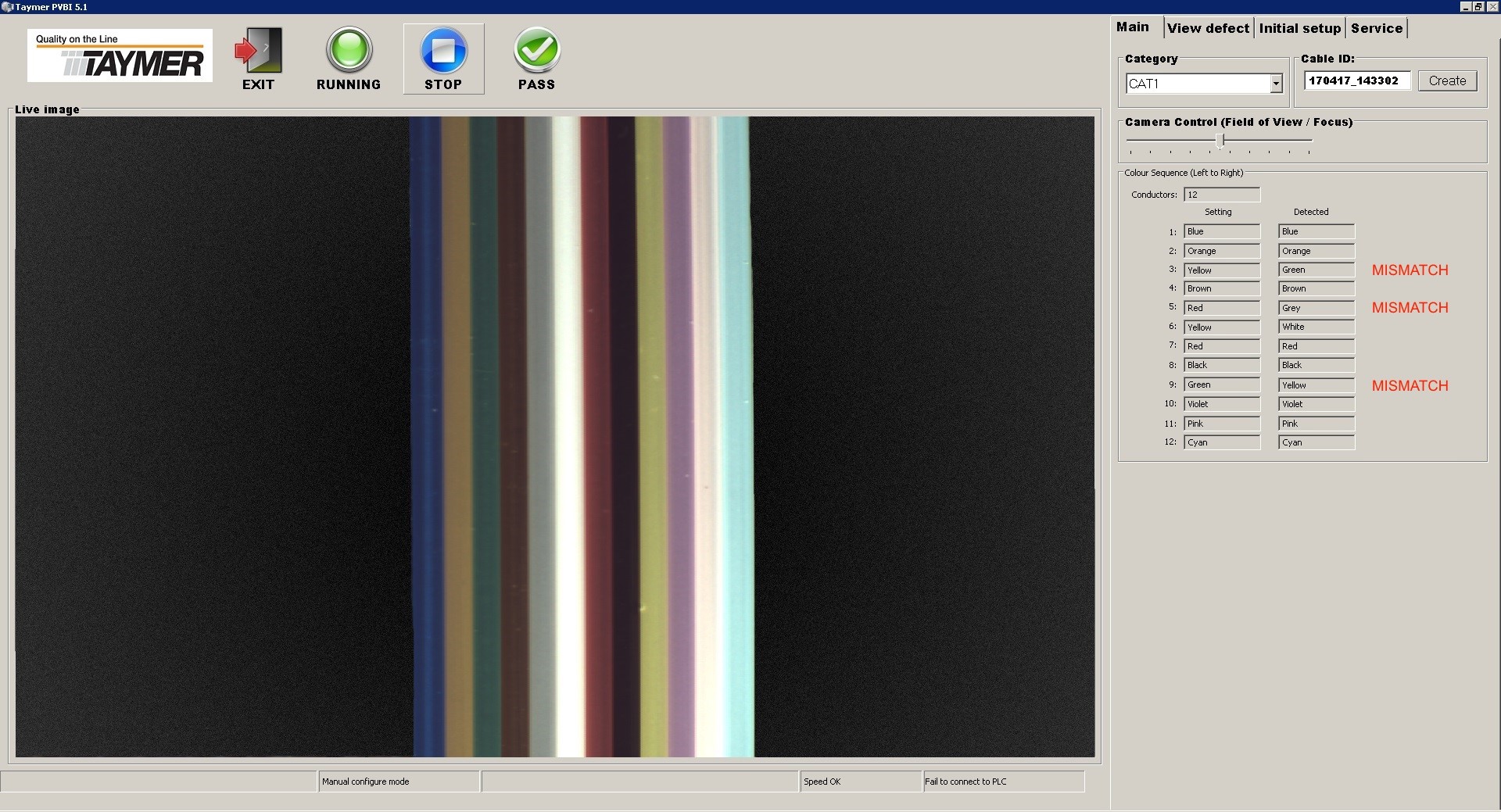
IWCS 2017 – Fiber Ribbon Dimensional Measurement and Color Sequence Verification
October 20, 2017IWCS 2016 – Print Length Verification for Cable
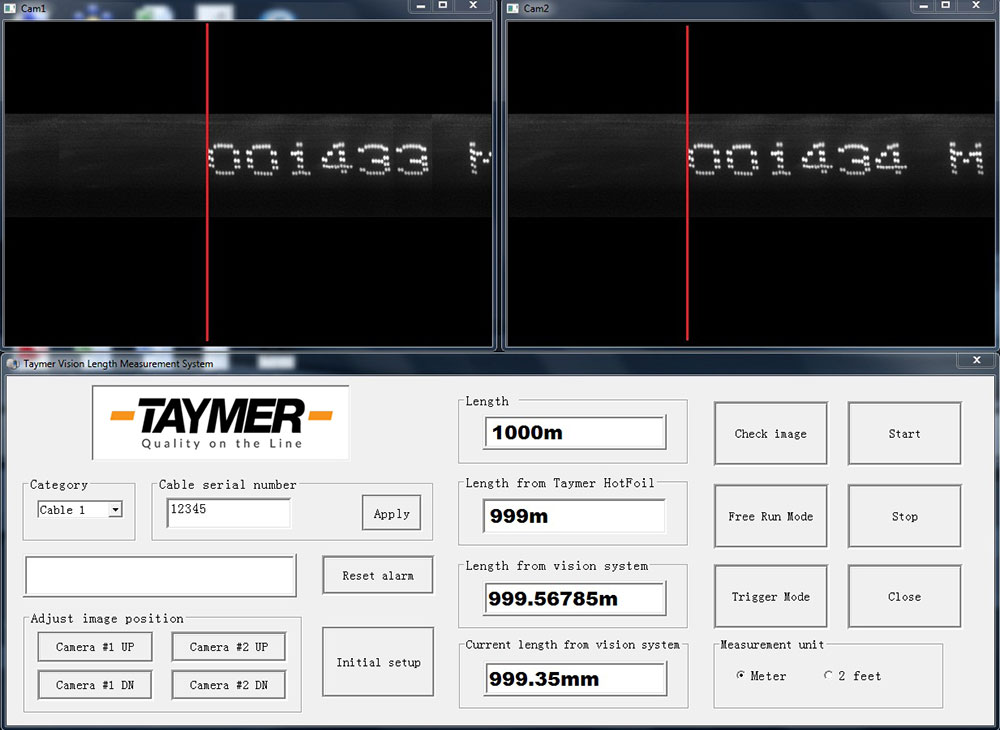
Print Length Verification System for Cable
Mr. Craig Girdwood, Mr. Andrew McCloskey
Taymer International Inc., Markham, Ontario, Canada, +1-905-479-2614
Abstract
Taymer’s Print Length Verification system is a tool that allows cable manufacturers to verify the feet or meter markings printed onto their product are exactly the correct distance apart. Cable is printed and customers typically buy product based on printed markings rather than true length. This system ensures this printed distance is accurate and the system can communicate with the printer to recalibrate the print interval if needed. Cable printed with incorrect printing intervals can lead to customer complaints and the manufacturer giving away excess cable. Over long cable lengths, having accurately printed cable can lead to significant cost savings.
Introduction
Long cable lengths are typically sequentially marked with incrementing count every 1 meter or 2 feet. These markings are used by the end user in various ways. Some products that are sequentially marked are fiber optic cable bundles and power cable. These markings can be produced by different printer types, including hot foil, ink jet, laser, indent/emboss and sinter. Accurate length markings is important due to customers purchase based on length and if in the field they find their product is inaccurately length marked they could be shorted cable and this can lead to complaints. The manufacturer providing length that is longer than what is marked will just be giving away cable for free. For long cable lengths this difference can be quite significant, and accurately printing can lead to substantial cost savings.
The Print Length Verification system can communicate with the cable printer and adjusts the print interval automatically based on the measurements removing the need for an operator to measure cable manually and adjusting the printer settings. This recalibration feature is essential to ensure consistent measurements through 100% of the cable length. The system measurements can be provided as an output to other equipment providing increased accuracy over a standard contact or laser length gauge.
The Print Length Verification system is able to be easily integrated into existing production lines and performs well for a variety of printer types and models including all Taymer hot foil printers and most models of inkjet printers. The Print length verification system makes sure that the printed length is accurate for the whole cable length and prevents incorrectly printed cable from being sent to customers.
The lifetime of the lights can be over 50,000 hours of usage and they are the only consumable part.
Current Print Length Accuracy Limitations
Encoder Measurements
Most inkjet, hot foil and laser printers on cable jacketing lines use encoder measurements to maintain print distance accuracy. Length measurements from encoders need to be recalibrated to ensure accuracy and if the accuracy is compromised there is no in-built verification. Sometimes the length measurements that the printer uses are from a different section of the line leading to a discrepancy between the cable length and the printed length.
A common occurrence in production lines is the encoder wheels experiencing slip on the product. This slip can be intermittent for short or long lengths and hard to notice by the operator. This can make even a well calibrated encoders measurements unreliable over the course of a run.
Operator Manually Measuring
A common technique that is used in manufacturing plants is an operator periodically measuring the print length using a ruler. This takes operators time and is potentially subject to human error. Measurements are also not done frequently potentially allowing significant amounts of cable to be marked with the incorrect length. If the incorrect length is found the print interval must be adjusted by the operator and then the print length must be re-measured to confirm accuracy.
Machine Vision Inspection System
Optical Mechanical Design
The Print Length Verification system (PLV) makes use of two high speed cameras synchronized to simultaneously capturing images of the cable surface. The camera and adequate lighting of the system allows capturing of images of the cable at speeds up to 1500 feet (450 meters) per minute.
The lighting varies depending on the application. The factors in consideration are the reflectivity of the material, surface profile, color, line speed and camera type.
The PLV technology uses an advanced algorithm to detect a repeating mark, or section of print that occurs at the printing interval. Typically this mark is the FT or M markings that are printed after the sequentially increasing number e.g. 503 FT and 504 FT. The PLV analyzes the images to locate the repeating marking and measures the distance from a calibrated reference point.
The PLV comes equipped with a certified ruler that is accurate to within ±0.08mm per meter. At any time an operator can easily move the ruler to the field of view of the cameras to check the calibration of the system. The calibration can be performed routinely to ensure the highest accuracy of the system, or if the desired print interval is changed.
When the PLV system is installed our engineers connect the system to the PLC of the printer. The PLV will continuously monitor the print interval and when the interval is outside the required tolerance the PLV will recalibrate the printer, by adjusting the length input provided by the internal/external encoder.
If a large print interval defect is detected, an alarm will notify your operator and an error report is saved to the ongoing data log.
Improving Quality Assurance
Suitable for any type of Optical Fiber Ribbon
Since the Print Length Verification system uses machine vision, it is able to be used measure the print interval for any type of product with a repeating legend. It is the most accurate and thorough method of measuring print intervals available and is the only system on the market that is able to automatically communicate and recalibrate the printer on the fly.
Reduce Printing Rework
The Print Length Verification’s Continuous Capture provides the operator with up to the second digital image feedback of the current print distance on any production line. This continuous stream of real time information allows the operator to monitor the print quality and gives him or her the time to react to correct marking problems before they result in expensive cleaning and reprinting or even scrapping of product.
Quality Assurance
Using the Print Length Verification, the user can save the lengths and calculations (Standard Deviation, 6sigma, etc.) to disk and print them out for quality reporting both internally and to customers. The Print Length Verification makes it possible for operators to verify print settings at shift changes and for engineering and production supervisors to verify the lengths while briefly walking past the operator’s console.
Limitations
There are a few limitations to the Print Length Verification system.
- The PLV requires a repeating mark/pattern that is always in the same position in the print legend e.g. “M” or “FT”. A section of text/numbers in the print legend can potentially be used provided it is not changing.
- The PLV requires space of 1 meter which can be difficult to fit in today’s production lines. It is possible to fit other equipment between the cameras so this space can be utilized fully.
Test Results
The Print Length Verification system is a modified version of the Print Verification system that is used in numerous production lines around the world to detect print defects and verify print legibility on wire and cable.
Some images of subsequent print markings can be seen below in Figures 1 and 2.
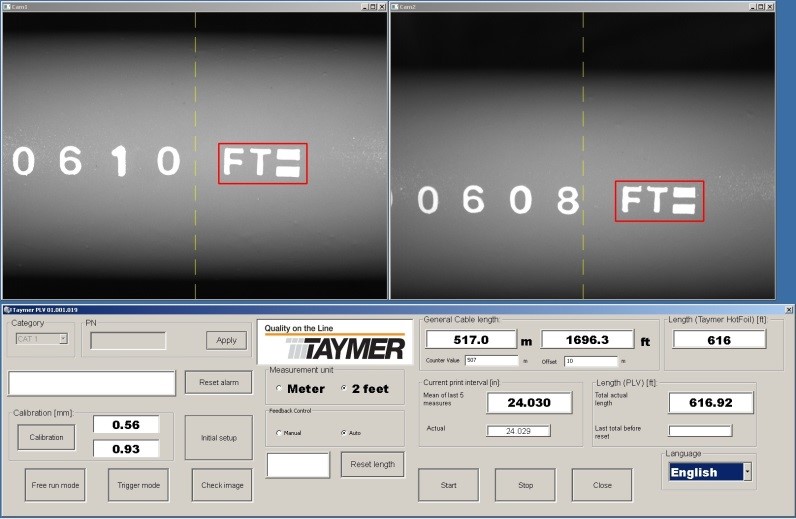
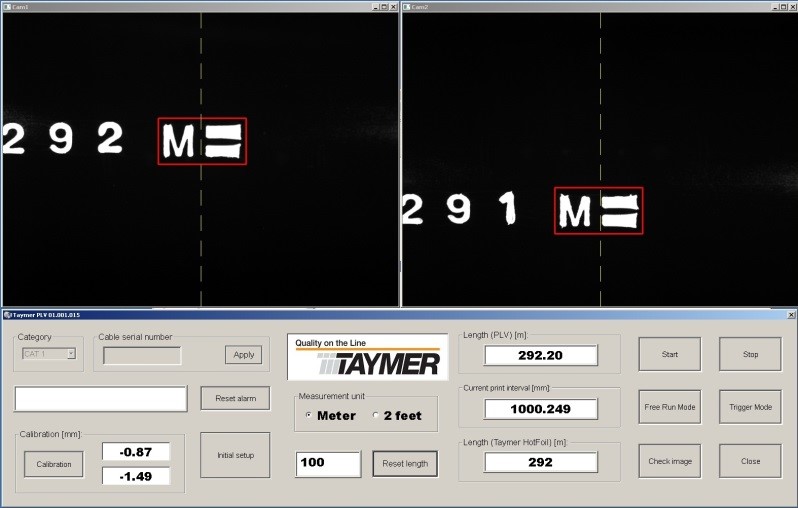
Conclusions
With a print length verification system, inaccuracies in the print interval cable surface will be detected and the printer will automatically be recalibrated by the system. The system provides several benefits.
- Suitable for any type of printed wire/ cable
- Improve Length Measurement Accuracy
- Reduce printing rework resulting in material cost and labor cost
- Increased Operator Productivity
- Continuous recalibration of the printer
Contact us today if you would like to discuss Taymer’s Print Length Verification technology further.